来源:中国石油新闻中心 时间:2017-11-27
寒冷冬日,管道翻山越岭、穿河跨江,载着滚滚“蓝金”,为千家万户送去温暖。你知道吗,这看起来又黑又粗的管道,绝非“傻大黑粗”之辈,而是满“管”的智慧与高科技。从制管到敷设再到运行,从选材到焊接再到投产,每一道工序的背后都有多重技术的支撑。今天,小编与您一起了解,管道中“隐匿”的那些黑科技。
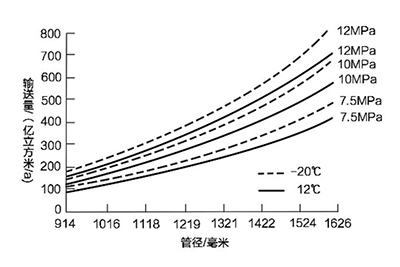
天然气管道输送量与输送压力、管径的关系
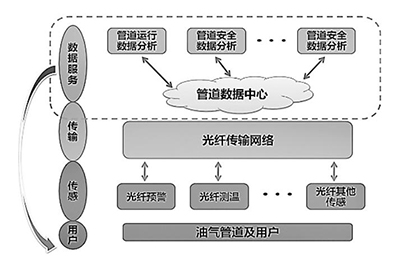
建设智慧管网
管材:强度与韧性的跨越
西气东输一线之前,我国陆上天然气管道输送压力最高为6.5兆帕,管线钢最高等级为X65。理论上,每提高一个钢级,建设成本可降低约7%,因此,随着天然气管道输量的提升和输送压力的增大,管线纲级实现了从X65到X70到X80的升级。目前,X90已具备批量生产能力,X100也已试制成功,我国高强度高韧性油气输送管制造技术和水平已经跨入世界先进行列。
【X80钢】高强高韧降成本
X80是高强度管线钢的美国分类型号。X80,即管线钢管最小屈服强度80kpsi(552兆帕)的前两位。
“十一五”至“十二五”期间,随着西气东输二线输送压力进一步提高,X80高强高韧管线钢管研发成功。包括大口径螺旋焊管、直缝焊管、热煨弯管、热拔三通管件等在内的X80钢管系列产品全部实现国产化,西二线干线、西三线全线等重大工程均采用该钢级钢管铺设,成为我国油气输送管材技术发展的一个标志。X80钢管是当前长输油气管道建设的主力产品。
为进一步提高管道工作压力,降低管线建设和运行成本,满足更大输量石油天然气管道建设的需求,耐压更高、强度更大、抗腐蚀能力更强、更省原料的新一代高性能油气管材——X90/X100焊接钢管成为研究重点。目前,宝鸡钢管、渤海装备等制管企业均已完成了X90/X100直缝、螺旋焊管和管件的试制工作,并具备X90批量生产能力。
【焊接工艺】“薄弱”环节不“弱”
焊缝是焊管上最“薄弱”的环节。为提高产品质量,保证管道安全运行,针对不同钢级大口径螺旋埋弧管的生产需要,研制出相应的焊接工艺及相匹配的焊丝、焊剂。特别是X80高速焊剂的成功开发与应用,使制管过程中焊接速度由原来的1.2米/分提升到1.7米/分,生产效率提高25%。
【抗大变形钢】能“变形”的钢管
随着天然气的开发向沙漠、极地和海洋等偏远地区延伸,长输管道不仅要经过冻土带、滑坡带、地震带、煤炭采空区等地质和气候条件十分复杂地区,而且还要在服役期间承受由于地面塌陷、移动引起的钢管变形。
为提高管道在极端地区的适应能力,确保安全平稳运行,国外在基于传统应力设计的基础上,提出了基于应变设计的理论。西二线在部分大变形地段首次引进使用了国外抗大变形管线钢管。
2009年,中国石油启动“西气东输二线管道工程关键技术”重大科技专项,国产X70、X80级抗大应变钢管研制相继取得重大突破,打破了国外同类产品的垄断。
设计:标准与优化的协奏
标准化设计在效率和产品质量上实现了大的提高。从效率角度来说,由于有原有设计成果可供借鉴,节省了大量的前期研究方案、布局的时间;从质量上来说,在借鉴之前成功设计经验的基础上,后续类似工程使用时,能够避免发生重复性错误,避免同类质量问题。
【管道设计】科学分类统一标准
针对不同类型的油气库站场进行科学分类,对工程建设中同类型站场、配套设施进行系统分析、总结共性、优化简化,并设计形成技术先进、通用性强、可重复使用的标准化、模块化、系列化设计文件。
管道局标准化设计相关工作包括管道板块的《油气储运项目设计规定》、技术标准、模块化设计、橇装化设计、装配式建筑、数字化管道设计。主要应用成果体现在线路标准设计、地质灾害系统化标准设计和管道穿跨越标准设计。
建设:速度与质量的突破
从八三管道的熬沥青补口到中俄二线的机械化补口和聚氨酯补口,从手工焊到半自动焊再到全自动焊……技术的进步不仅解放了人力,而且让管道建设提质提速提效。
【全自动焊】“机器人”焊接又快又稳
上世纪70年代之后的20年里,我国的管道焊接技术以手工电弧焊为主,效率低,质量受工人技能因素影响大。从西气东输工程开始,我国高强管线钢大面积应用,自动焊技术装备逐渐成为管道施工的主流焊接技术。
自动焊技术是一种集计算机、自动控制、信息处理、机械和电气于一体的复杂材料成型加工工艺过程,被业界称为管道领域的焊接机器人。自动焊剔除了人为干扰的因素,能够保证焊缝质量的稳定性和一致性。目前,管道局结合施工实际需要,研制了低温版、大坡度版等不同种类的产品。低温版的CPP900可应对零下40摄氏度的极寒环境,大坡度版则可以在30度坡度条件下进行上下坡平稳行走和焊接施工。
【机组通】扫个码,施工全程可追溯
机组通是管道局自主研发的“工程项目现场数据采集系统”,承载于一部加强的平板电脑,实时记录施工一线的300余项数据,还可让重复数据自动关联。机组通采集的数据,让深埋地下的管道显性化。管道出现故障时,扫一扫贴于管道外壁的二维码,维修人员便能轻松查到所有同批次配件的安装位置,甚至安装工姓名、监理姓名、安装时间等信息,实现了“一机在手,数据全有”。
【通信】管道“经络”畅通无阻
与管道紧紧依偎的光缆是管道的神经。光缆是保证管道通信畅通的载体。智慧管道离不开神经系统的支撑,主要包括光缆传输、光纤预警、光纤传感和光纤应用。
随着大数据的发展,光纤应用向着更加先进的方向发展,光纤应用Plus将在大数据中有更广泛的应用,形成完善的管道光纤神经网络。
【防腐】从“人工刮胡子”到机械化喷涂
八三管道建设时期,管道防腐要把沥青熬成“汤”,两人用布兜住焊口来回拽,一个人往焊口上浇沥青。这种刮胡子般的补口方式要3个人才能完成。如今,已经在很多重点工程项目中大规模应用的热收缩带机械化补口装备,只需1个人便可完成从喷砂到红外加热的3道工序,实现机械化补口。
热收缩带机械化补口技术彻底解决了传统手工热收缩带补口存在的质量不可控、人为因素影响大、施工效率低、工人劳动强度大且安全隐患大、作业环境差等问题。
机械化液体聚氨酯补口喷涂机的诞生,使涂料、溶剂等操作在完全密闭条件下进行,把工人与涂料等暴露接触时间降到最短。
管理:距离与效率的升级
【SCADA系统】管道运行实时监控
SCADA系统是以计算机为基础的生产过程控制与调度自动化系统,可对现场运行设备进行监视和控制。SCADA系统软件通过PLC(可编程逻辑控制器),将现场仪表采集和获取的管道及其附属设备的运行状态数据以文字、动画等形式显示出来,从而实现对管道运行状态的监视,也可将控制命令通过PLC发给现场的开关、阀门等设备,以实现对管道压力、流量、温度等自动控制。
【全方位超高清漏磁内检测】缺陷“一网打尽”
目前,管道内检测通常使用传统轴向漏磁内检测器。这种内检测器只能识别沿管道周向方向的缺陷,而对于沿轴向方向缺陷的识别“无能为力”。全方位高清漏磁内检测器在继承传统漏磁检测器优点的基础上,可以识别沿管道轴向方向的缺陷。经过一次检测,管道各个方向的缺陷均可以“一网打尽”,提高了管道的检测效率。(陈青、李程、尹竞采访整理)
技术故事
控制焊缝高度:毫厘之间见功夫
11月23日上午,集团公司焊接技能专家胡德虎照例去宝鸡钢管输送管公司螺旋焊管生产线查看并了解情况。进厂工作30多年来,如何有效控制成型和焊接质量、提高生产效率,是这位“身怀绝技”的高级技师琢磨最多的事。
看着刚下线的钢管上长长的焊缝平缓光滑、边沿整齐,胡师傅告诉记者:“现在,我们的大口径厚壁螺旋焊管焊缝高度基本比行业标准低0.7毫米。”
说起来只有零点几毫米的差距,然而,为了这“毫厘之间”的精准,几十年来,宝鸡石油钢管有限责任公司的技术专家和操作人员不知付出了多少心血。
螺旋焊管是一种传统产品,同一宽度的卷板可以生产不同直径钢管,最突出的难点是如何控制焊缝高度、管端椭圆度及管径偏差等。
“自动焊接是螺旋焊管制造的关键技术之一。”输送管公司制管三分厂技术组组长胡绪波告诉记者,在高钢级大口径大壁厚螺旋焊管生产中,任何焊接质量波动,都会造成整个生产线堵塞,影响生产进度,降低效率,增加成本。拿焊缝高度超标来说,不仅影响产品外观,而且会给管道施工现场的管对管接焊带来困难。另外,钢管做3层结构聚乙烯防腐时,还需要全管体加厚涂层,焊缝高度超标会大大增加防腐材料的用量。
“准确控制焊接熔深和内外焊偏移量,是决定埋弧焊接焊缝质量的关键。”胡德虎告诉记者。
近年来,宝鸡钢管对不同原料采用不同的双丝高速焊工艺参数,并通过优化调整焊丝倾角、板边坡口等方法,使大口径高钢级螺旋焊管的焊缝高度基本控制在1.8毫米以内,焊速保持在1.7米/分左右,焊接效率提升30%以上,焊缝一次通过率达到98%。同时,管径偏差小于3毫米,管端椭圆度达到同规格直缝焊管水平。(陈青王冠慈)
机械化补口:12分钟完成一道管口
在正在建设的中俄东线施工现场,记者看见的是一片热火朝天的施工场景。然而,与西气东输一线、二线工程不同的是,工人们手持火把挥汗如雨地炙烤防腐补口带的画面不见了,取而代之的是管道局自主研发的防腐新技术装备——机械化补口装备。
机械化补口技术以专用于热收缩带补口的机械化装备为基础,结合相应的施工工艺完成补口作业。主要装备由环保型密闭喷砂装备、中频加热设备、红外加热装备及配套的动力、行走装备组成。
管道研究院施工装备研究所王长江告诉记者,为解决传统手工热收缩带防腐补口技术存在的补口质量不可控、人为因素影响大、施工效率低、资源浪费、劳动强度大等问题,机械化防腐补口应运而生。
12分钟,这是在工况良好状态下,机械化补口每道管口完成一系列工序所需要的时间。而同样一道管径1422毫米的管口,手工防腐补口要40分钟。中俄东线技术人员介绍,每公里约80道管口,采用机械化补口比手工补口缩短4至5天。
“工程实际应用证明,机械化补口是管道建设的助力器。但国内的机械化补口技术研发还面临瓶颈。”王长江说,机械化补口设备庞大,灵活性远不如手工补口,而且其对地形要求和运行成本相对较高,这些因素大大制约了机械化补口的规模化应用。
“现在急需解决的问题是机械化设备的集成化、小型化,把设备的功能进行集成,这个课题已经开始研究。下一步研究重点包括机械化补口装备高寒低温环境的适应性等。”王长江告诉记者,他们对于机械化补口还有很多设想。(李元滢李程)
CPP900:比肩国际“最先进”
在焊接行业拥有自己的技术,是管道研究院施工装备研究所所长尹铁的梦想。随着管道局科研团队研制的CPP900系列自动焊装备问世,尹铁的梦想终于实现了。
“在管道焊接,尤其是大口径管道焊接方面,CPP900不仅会提高焊接质量,而且能够提升施工效率,给工程带来安全和节能。以CPP900-1422大口径坡口机为例,其坡口尺寸误差小于0.1毫米,平面度误差小于0.05毫米。”尹铁自豪地说。
尹铁告诉记者,管道局曾经引进国外的自动焊装备,价格昂贵,后续服务成本高,而且引进技术基本不可能。为避免在管道施工关键技术上受制于人,尹铁和他的科研团队走上了自主创新之路。
主控板是自动焊的大脑,也是核心技术。CPP900主控板的电路板由管道局技术人员自己设计,控制程序由技术人员自己编写。技术人员更是让CPP900实现了焊缝自动跟踪功能。这个技术可以使焊缝不容易出现缺陷,能保证焊接的精度和质量。
此外,科研团队对CPP900的焊接小车、电源、导向轨道等都重新设计。以前,如果想修改主控板内的焊接参数,需要专业技术人员用笔记本连接设备进行操作。如今的CPP900,焊工可以根据不同的现场环境,随时在触摸屏上修改存储焊接参数。这样一来,整个控制系统的适应性更强了,设计更人性化。
在试验操作中,CPP900坡口机的坡口尺寸误差、坡口平面度误差与世界最先进的美国CRC坡口机同步,而CPP900单口加工时间更短;内焊机与CRC性能参数同步,而CPP900单口焊接时间更短,自爬坡能力更强;外焊机性能达到CRC水平,对口间隙与坡口误差适应性更宽。(李元滢李程)
管道内检测:两次失败换来国际首例
10月11日,这一天对于西部管道公司来说是个大日子:全方位超高清漏磁内检测器在西三线了墩站至烟墩站成功运行,检测数据完整有效。“这是国际首例!以前做检测要么采用轴向,要么采用周项,我们这个检测采用了轴向和周项相结合的方式,以前没有过!”收获的喜悦洋溢在公司科技信息服务中心完整性所耿丽媛的脸上。
5年间,耿丽媛见证了业界第一台大口径高压输气管道全方位检测器从投产失败到数据成功采集的全过程。
2013年,为解决目前管道内检测通常使用的传统轴向漏磁内检测器无法有效检出轴向缺陷、焊缝裂纹等检测精度亟待提高的问题,西部管道科技信息服务中心立下愚公志——研制出全方位超高清漏磁内检测器。
从无到有,从有到精,从完成设备制造到现场试验,从前期设计、技术难点攻关到设备成型,经历了数次试验和调试。
对于现场反复试验的那段日子,耿丽媛说她一辈子都不会忘。第一次试验是在西二线了墩站发球,182公里外的烟墩站接收检测器,检测器长6.5米左右,重量达7.5吨。检测器从了墩站进入管道到达烟墩站,大概需要13个小时。第一次试验,因后节支撑皮泄流孔较小,检测器后节倾斜,电源线断裂,无法有效采集数据。
时隔近一年后再次试验。这次试验,耿丽媛将自己的整个夏季记忆留在了戈壁滩上。夏季的戈壁滩最高温度达45摄氏度左右,耿丽媛不分昼夜全程监督检测器的拆卸和安装,终于在5天内完成了检测器的重新组装,具备发送检测条件。发送成功后,耿丽媛和同事们开始跟踪作业,在戈壁滩上一待就是一天一夜。然而,因中暑住进医院的耿丽媛收到了喜忧参半的消息:检测器收取完好,部分数据采集出现问题。
虽然经历了两次失败,但是科技信息服务中心的科技人员经过不懈努力,终于在今年10月11日,体验到了收获的喜悦。